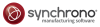
GIW Industries, a KSB subsidiary in the U.S., implemented Synchrono® SyncManufacturing, demand-driven production planning, scheduling and execution software in their facility. GIW's main demand was based on manufacturing slurry pumps for dredging work. Prior to implementation of Syncrhono software, on-time performance was 45%, cycle times were 18 to 20 weeks, and inventory turns were 4.5. Today GIW uses Synchrono SyncManufacturing software to optimize product flow and assist in controlling cycle times and delivery performance. The system integrates pattern information, flask, combination equipment, engineering revisions and capacity to produce a schedule that is predictable and reliable.